The extreme hardness and resistance of wear plates such as Hardox, Creusabro, Abro, Raex, Strenx and Bissalloy make machining particularly challenging.
To ensure successful machining of wear plates, our Alpha VersaDrive cutters and countersinks have specific recommendations that must be followed.
Good results depend on the correct setup, including high torque, slow speed, geared magnet drills, and a generous amount of cutting fluid like the Alpha C.D.T Cutting Lubricant.
An incorrect and poorly maintained magnet drill with an unstable drilling operation, poor magnet hold, excessive pressure or inadequate lubrication will likely result in immediate tool failure.
Correct usage and setup are critical, and a warranty will not be given unless proof of correct use can be provided.
Alpha VersaDrive CarbideMax TCT Broach Cutters
The Alpha VersaDrive CarbideMax TCT Broach Cutters are specifically designed for the toughest broaching tools. The specialist ultra-coating significantly increases tool life when working with extremely hard materials and wear plates.
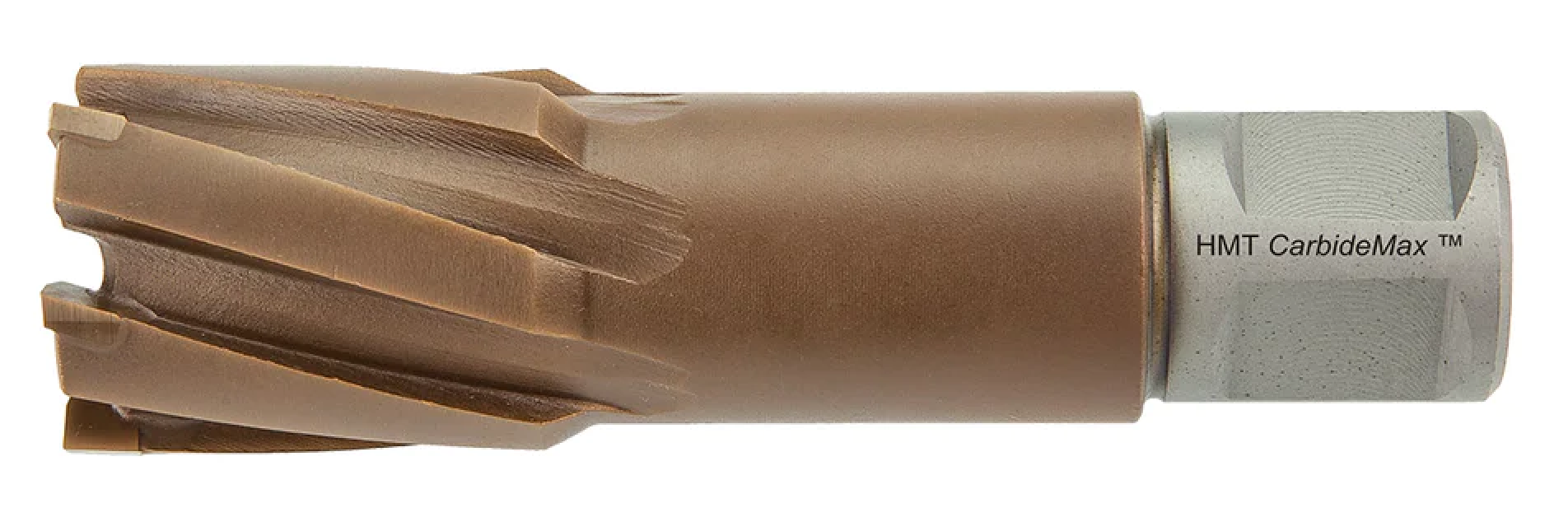
Broaching Best Practice Advice:
- Cautious and gentle feed pressure should be used at all times, especially during the start of the cut and exiting the material.
- Generous application of Alpha C.D.T Cutting Lubricant should be used during the cut and applied frequently during the cut with thorough cutter coolant supply if possible.
- Backing off the cutter and applying more lubricant is necessary for increasing tool life.
- Swarf removal from the cutter can assist with longer tool life.
- For best results, use a powerful magnet drill with high torque and low gear speed such as the V100T and V125T machines.
Alpha VersaDrive Weldon Shank TCT Countersink ULTRA Coated
The Alpha VersaDrive Weldon Shank TCT Countersink ULTRA Coated has fully ground flutes and titanium nitride coating to help reduce wear and blunting. This enables quick deburring and countersinking of holes up to 16.5mm with minimal torque kickback.
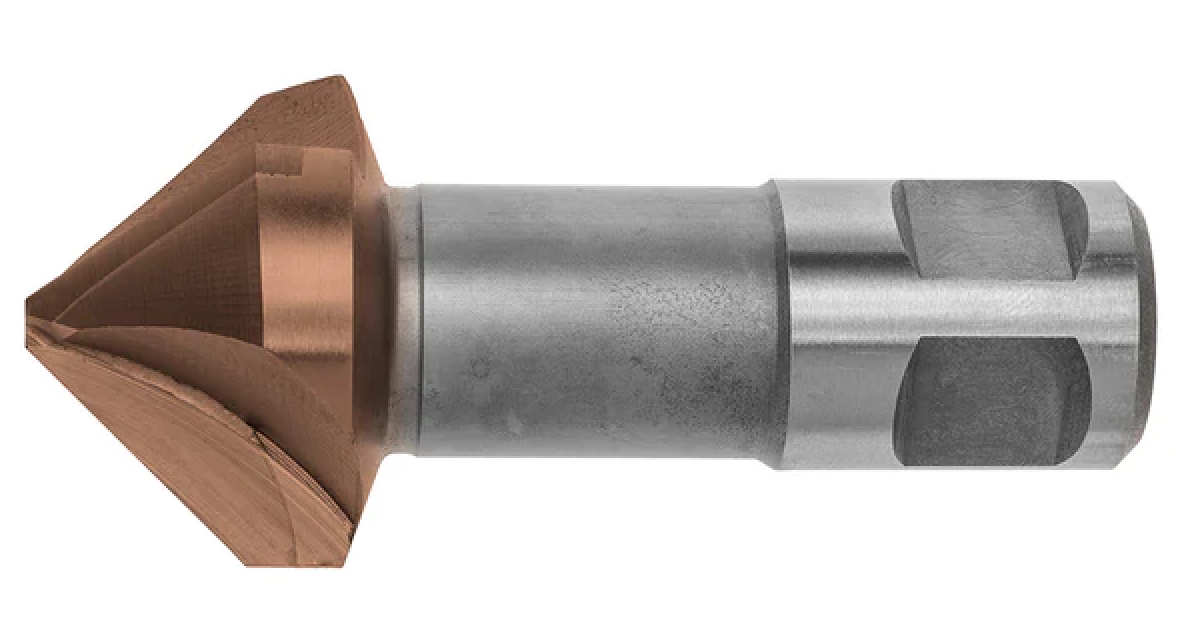
Countersinking Best Practice Advice:
- For best results the countersink should be piloted where possible.
- Do not allow the countersink to vibrate over swarf while cutting as this will cause chatter, ultimately causing the cutting edes to hip and blunt.
- Regular lubrication and swarf removal on countersinking is essential.
- A hand brush works better than mag stick to clean cutter and material surface.
- For best results, use a powerful magnet drill with high torque and low gear speed such as the V100T and V125T machines.
Sheffield Group’s Hot Tips:
- Make sure the mag-based machine can machine Bisalloy, e.g. can gear down low enough in RPM, has a strong magnetic hold, and minimal play in the slideway.
- Rigidity is key.
- When using a geared drilling machine, use low gears to provide maximum torque
- Speed should be lowered when using a magnet drill with electronic torque control.